Vacuum forming
Vacuum forming is a low cost and efficient method of creating products from plastic. Our plastic vacuum forming services can be used for a whole range of applications from small intricate machine parts to large scale manufacture; vacuum formed products are found in every walk of life.
Due to the cost effectiveness, flexibility and speed of production that can be obtained from this type of thermoforming it is no wonder that vacuum forming is so popular and is preferred to other more complex methods of thermoforming such as injection moulding.
GET IN TOUCH
Get a free no obligation quote or some friendly advice from our team.
WHY CHOOSE US?
Reduced costs
We are proud to say that we are very competitively priced but we never compromise on quality. We are careful to minimise material wastage, use the most cost effective type and grade of plastic, and where possible we design tooling to be multi impression meaning that a number of products are produced with each machine cycle.
NO MINIMUM ORDER
With reduced tooling costs and our efficient automated process we are able to make low volume manufacturing cost effective and possible. We enjoy the challenge of low production runs and are often involved in producing one-off products, this is often the case in the movie industry for example. We are as comfortable with a run of one product as we are with a run of ten thousand or more!
HIGH VOLUME MANUFACTURING
Vacuum forming lends itself to high volume manufacturing. Whilst we love and enjoy the lower volume specialist jobs, over 70% of our work comes from high volume repeat orders and we are geared up to deliver on these and are consistently delivering on time and to specification. No wonder we have such a loyal and long standing customer base.
MATERIALS
The majority of jobs tend to be formed from traditional oil based plastics. However, it’s a changing world so we already quote recycled material wherever possible – this brings cost savings and of course means you are doing your bit for the environment. As a rule of thumb a recycled material can be 20% less expensive than a comparable virgin material but the depreciation in overall strength is only 6%. It is early days for bio compostable materials but we are already working with these and have been involved in the testing and development of Bio’s. There is a huge swing towards recycled and bio material, and we understand the pros and cons (there are some cons) of these materials and can advise you. Regardless of material choice there are a wide range of finishes available from standard glosses, satins and matts in any pantone through to specialist carbon fibre, wood grain, metallic and one off finishes. Surface finish can be smooth, pinseal (slight grain), soft touch or even in a leather grain. Specialist material properties range from fire retardant, high temperature, UV stable, anti bacterial and food grade to name just a few.
Vacuum forming process
Thermoplastic vacuum forming is a technique for transforming flat plastic into a three dimensional shape using a mould tool.
Sheet plastic is heated to make the plastic malleable, then it is stretched over the mould tool and a vacuum is created as air is removed from the machine. The atmospheric pressure around the tool forces the plastic to cast itself upon the tool, producing the plastic silhouette.
Excess plastic is removed by the CNC (Computer Numerically Control) machines and then the product is ready to travel through to its next stage of production, whether that is fabrication and assembly, or to be sent to the client as a finished plastic product.
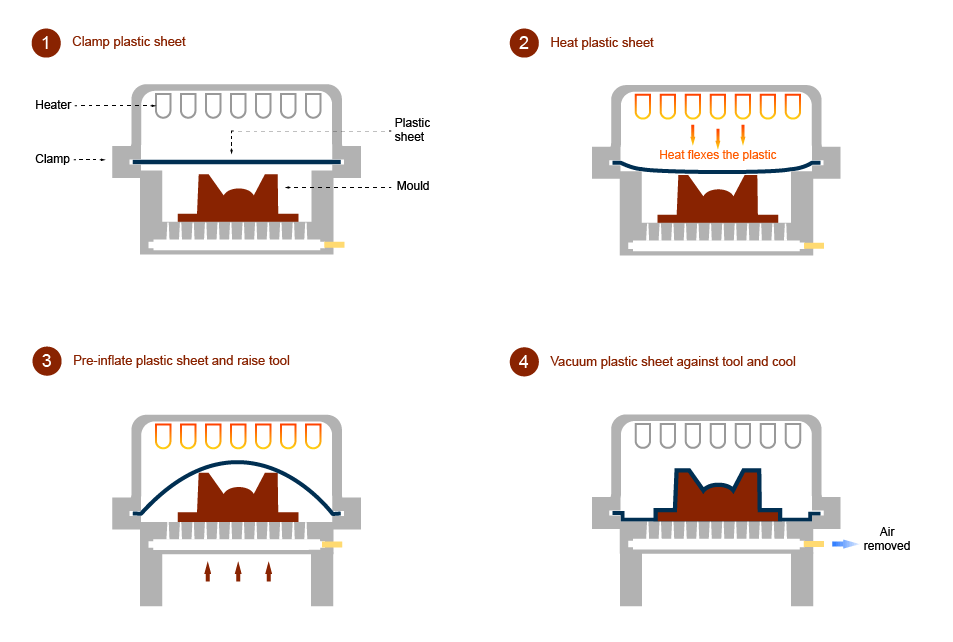